Transfer Decoration with a Difference – it’s time to Double-Up
When asked to write the transfer column this month in an edition about urban clothing we thought we’d try and do something a bit different.
I think it’s fair to say that when we look at garments online or in a shop that have been decorated in multiple positions ,we assume that they have been achieved using industrial printing equipment and sometimes pieces of the fabric have been printed separately before the garment is stitched together.
We’re here to show you how you can achieve multiple layers of print, in unusual places across two pieces of clothing using very simple garment decoration processes to achieve high-value desirable finished garments. Firstly, we took our inspiration from Pinterest, see image 1. Then, we choose two technologies in our portfolio which are both cost effective and versatile processes that all garment decoration businesses should consider.
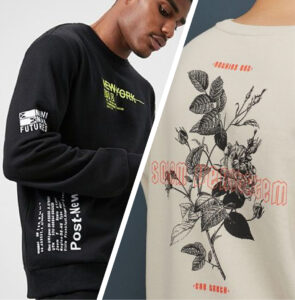
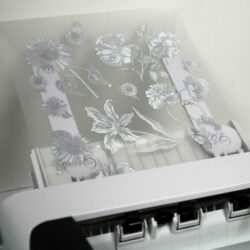
Step One – Full Colour Transfer
We found the background artwork on Freepic. This has been printed on the Oki Pro8432WT White Toner Printer with the Forever Laser Dark No Cut Transfer paper, and NEW B Paper PRO. This image has been Rasterised using the Forever RIP software, where the image has had a mask of different shaped holes strategically placed over the design. This process is great for many reasons including making the transfer feel softer, for better washability, durability, and stretchability, with an additional cost saving benefit in the amount of ink used. As a side note, as we are producing a ‘doubled up transfer’ having this transfer thinner is really important as it will give the final garment a fashion feel and add value to your end product.
The B Paper PRO product is the latest development from Forever. This product gives you an intense white and even better washability, stretchability and durability all for the same price.
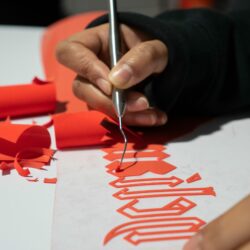
Step Two – Pop of Vinyl
Created using the Roland GS2-24 Vinyl cutter and a high pile premium neon orange flock vinyl for extra density. It has been cut using a 45–60-degree blade, so that the cut is precision perfect. The design then needs to be weeded, so that all the unwanted areas of the design are taken away.
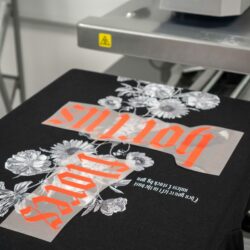
Step Three – Double it Up
Firstly, we printed the white toner transfer onto the garment as the base, which is a thirty second application and cold peel. Once this has been applied and the backing peeled, make sure that the garment with the other half of the transfer is flat on the heat press, as this is key to the second transfer pressing correctly. Then, very carefully move the flock transfer into position over the original print. At this point we also recommend using some heat tape to hold the design in place, so that it does not move when you lock the press down and also cover the rest of the print with protection paper. It is best to have minimum vinyl backing around your text and then apply for the recommended time, in this case 15 seconds.
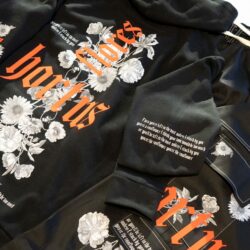
Once this is done you can remove the clear vinyl carrier sheet and hey presto you have your masterpiece for all to see!!
This is just our example. The base artwork could have been really bright full colour rather than the greys and whites we choose, and it may be that you use a Metallic HTV or one of the stamping foils for the second part of a design. Here we used two A3 sheets of heat transfer paper, plus 25cm x 50cm wide flock vinyl to decorate one hoody in five positions and a pair of trousers in two positions. The total materials cost for this feature was £6.20. For me, the hoody alone could be sold for £50 particularly if the design offered is personalised in someway to the customer’s requirement.
Adding value and being creative like this means you can obviously charge more for the final garment, but you will also stand out compared with your competition and this can attract you new clients and more orders.
If you need any help on how to achieve this give one of our transfer team a call, they will be happy to talk you through it.