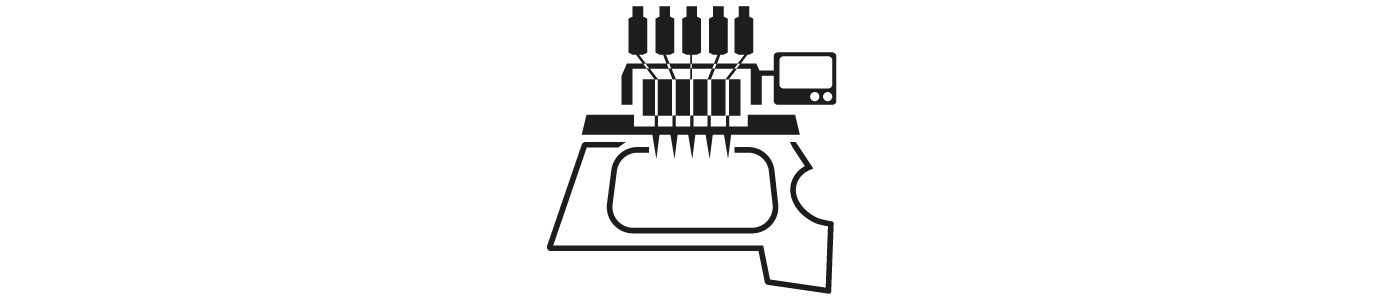
Melco
Modular embroidery machines from Melco
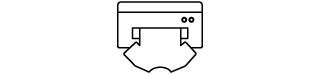
PolyPrint
TexJet range of DTG printers and pre-treatment machines
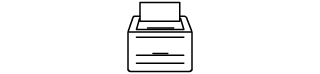
OKI
White toner printers for self-weeding transfer printing
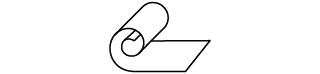
SEF
Cuttable and printable heat transfer vinyl
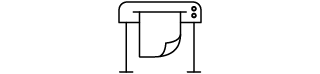
Roland DG
Print & cut, UV and DTF printers
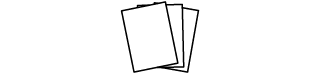
Forever
Laser transfer papers
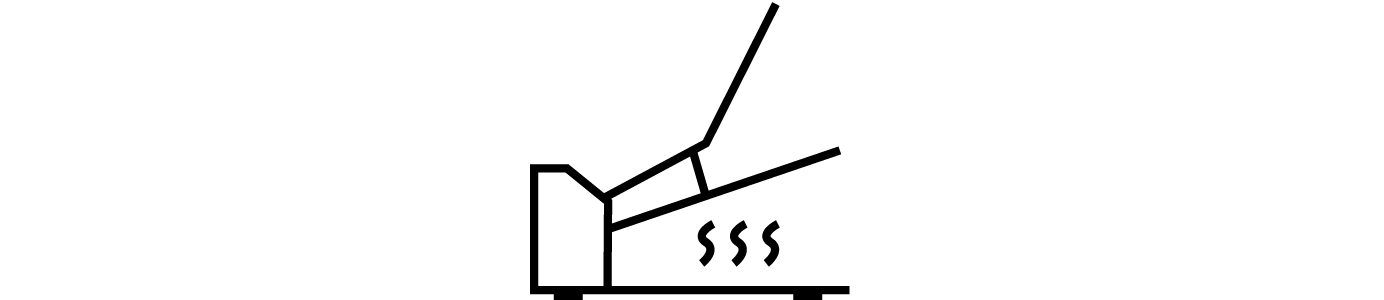